Blades are essential part of wind turbines, which are susceptible to various damages caused by environmental factors such as lightning strike or a simple wear-and-tear process leading to corrosion, cracking, and perforations. Sometimes, the major cause of blade damage is undetected manufacturing defects.
Regardless of the source of damage, if left unattended, it worsens with time under the stresses of turbine operation. Damages to the rotor blades affect the strength and inertia of the turbine, ultimately making power generation less effective and unreliable. Once damages form, if they remain undetected and are not remedied in a timely manner, they may lead to even higher costs, extended downtime, and potentially blade failure. A major failure of wind turbine blades can result in the reduction of the production, as the whole unit could be out of service.
With a proper monitoring such problems can be flagged on time, before they cause any major failure or early enough to address them during the manufacturer’s warranty period.
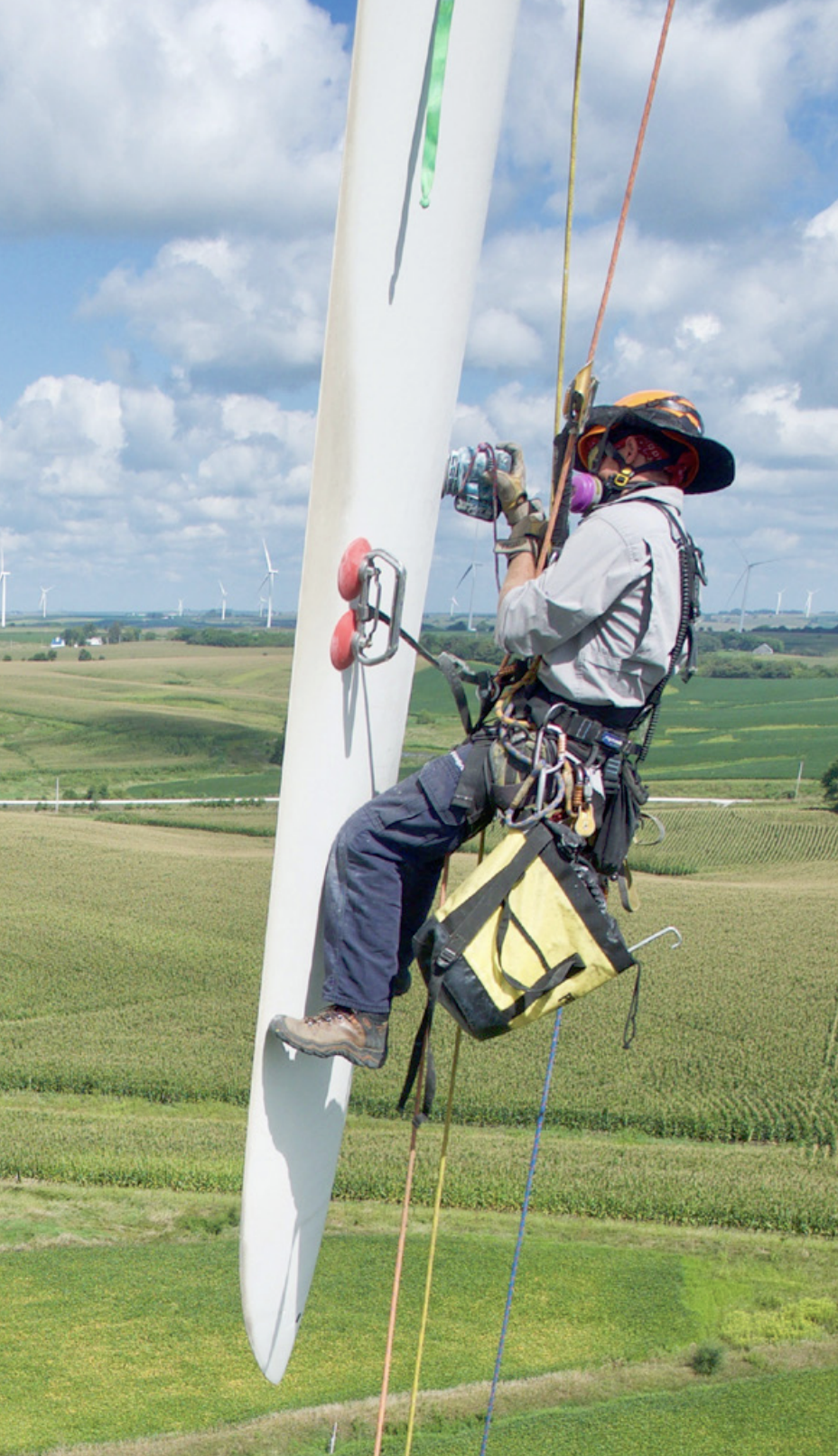
Source: Sensoria Guide “How to Drive Operational Excellence Through Blade Management”
Monitoring can be effectively boosted by modern technologies. Proper technologies can detect rupture, perforations, cracks, delaminations, impacts of lightning strikes, bond line failures, and serial manufacturing defects. Moreover, they can monitor the risk of developing failures and compare “health” of the blades within a farm. Those technologies, such as the Sensoria™ wind blade monitor from MISTRAS Group, involve acoustic emission technology (AE), with the acoustic data being collected by the sensors and data acquisition system installed on a turbine. Rope access technicians install one sensor in each turbine blade, which operate continuously 24/7/365. The sensors are “listening” for changes in the structure of blades to indicate a crack, rupture, or other damages. Once such abnormality is detected, the sensor sends this information to data acquisition box installed in the hub of the turbine. Then, data on the wind blade integrity is being transferred to the web-based data portal to help operators to make more informed decisions on inspection and maintenance, so they could see which blades require immediate assistance and which can wait.
Such a process of monitoring parameters of machinery in order to identify changes that are leading to developing a fault, is called Condition monitoring (CM). It relies on real-time sensor measurements, with outputs used to optimize maintenance operations and usage of resources.
Data acquired through the monitoring technology may be accessed via a convenient web application, such as offered by Sensoria. The Sensoria Insights web application enables operators to view blade integrity data at anytime from anywhere. “When damages are detected and confirmed, the portal sends notifications to operators to alert them of potential integrity issues, with all data collected from the sensors accessible through the Insights portal,” Sensoria explains on its website, adding that real-time alerts and mobile accessibility make accessing blade integrity data portal “as simple as checking your phone.”